Notable Features |
|
 |
Construction waste
reduction/recycling program |
 |
Reduced
construction waste due
to use of factory manufactured precast concrete elements |
 |
Application of
large panel steel formwork |
 |
Use of drywall for
the internal partitions |
 |
Use of aluminium slab
formwork |
 |
Use of precast facade |
 |
Use of precast
staircase |
 |
Use of precast
cooking bench |
 |
Use of
prefabricated door sets |
 |
Use of spray plastering |
 |
Use of gondola to
apply external finishes |
 |
On-site sorting of
waste |
 |
The
wastage for concrete was 2.5%. |
 |
The
wastage for reinforcement was 8 %. |
 |
The
wastage for tiling was 5%. |
 |
Metal containers
were used for site office |
 |
Reuse of surplus
steel bars |
 |
Reuse of
corrugated steel
hoarding |
Basic
Information |
|
 |
Location: Shek
Yam |
 |
Building Type: Residential |
 |
Contract Period: 27
months |
 |
Gross
Floor Area: 109,449m2 |
 |
Client: The Hong
Kong Housing Authority |
 |
Architect: Dennis
Lau & Ng Chun Man |
 |
Structural Engineer:
Maunsell Consultant Asia Ltd. |
 |
E&M
Consultant: Parsons Brinckerhoff (Asia) Ltd. |
 |
Quantity Surveyor: Frank
& Vargeson (H.K.) Ltd. |
 |
Main Contractor: Shui
On Building Contractors Ltd. |
 |
Contract Sum: HK$
780 million |
Overview |
|
The
Shek Yam Estate
Phase 3 was a residential building project and
the following major items were executed under this contract: |
|
 |
Four
41-storeys Concord Blocks |
 |
One multi-storey
carpark building |
 |
One
pedestrian footbridge |
 |
All
associated drainage and external works |
 |
Road
widening and lay-bys |
|
|
|
|
Plastering and Finishing
|
|
|
|
Since
the precast wall and floor slabs, as well as the factory
made internal walls provided a very smooth and accurate
surface, thick plaster was not necessary. Plaster
dropping on floor during the finishing process,
sometimes accumulate to a thickness of 30mm over the
whole floor area, can hardly be avoided in traditional
cement sand plaster. However this situation was not
happened, as sprayed plastering was adopted on this
site. |
|
|
|
|

|
|
Waste Management |
|
|
|
 |
On-site
sorting of waste |
|
|
|
Separation
of waste was not performed on site except soil was stored
separately for backfilling of external works. Steel refuse
chute was installed to discharge the waste material to the
ground floor for each block. However, there was no separation
of paper, cans, lunch boxes, plastic conduits and rubble, etc.
The problems associated with separation of waste on site were
the extra labour required and extra trucks required for
different types of waste. If on-site sorting of waste was to be
carried out, distributed separation was preferred. It was also
suggested to use two outlets at ground floor to facilitate the
discharge of different types of waste. |
|
|
|
 |
Material
Control |
|
|
|
|
|
|
|
 |
Use
of recycled materials |
|
|
|

|
Waste
water was discharged to the waste water treatment plant
and the treated water was distributed to the
automatic tire washer and used for ground washing. |
|
|
|
|
 |
Reusable
materials
|
|
|
|

|
Corrugated steel hoarding |

|
Metal containers
were used for site office |

|
Surplus reinforcement
was collected for reuse |
|
|

|
|
|
|
![]() |
|
Wall System |
|
Large panel
steel formwork was used to construct load-bearing walls of standard
domestic floors. |
|
|

|
Dry Wall |
|
The
internal partitions were built of factory made lightweight concrete
panels. Joints were minimized by the use of large size
floor-to-ceiling panels. Cutting was not necessary because the size
of the panels was tailored to suit the building, thus the amount of
waste that would be produced during construction was further
minimized. The time required was also less than the traditional brick
or block construction. |
|
The
factory made panel gave very smooth and accurate surface finish.
However, it might not be acceptable because of its lower strength in
supporting point load and resistance to impact. |
|

|
Slab
System |
|
 |
Aluminium slab formwork
|
|
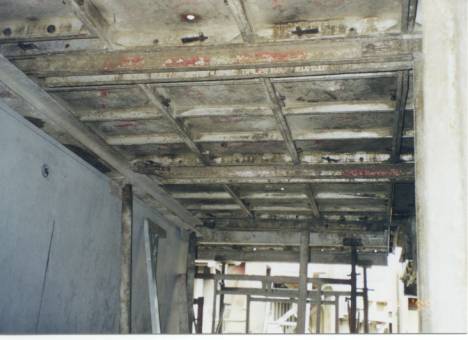
|
|
A 6-day floor cycle was
adopted. This speed was
more or less the same as those for private sector using
traditional methods. However, the aluminium formwork could be
used for three sites. It was considered cost effective to adopt
aluminium formwork. |
|
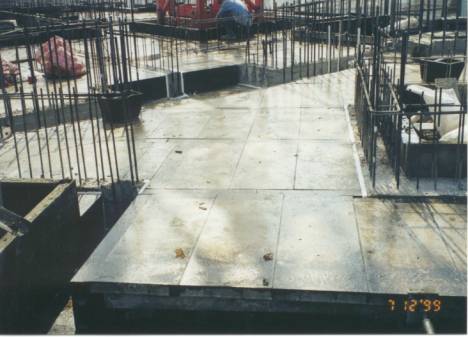
|
|
|

|
Precast
Facade |
|
The
precast facade was manufactured in China and transported to the site
for fixing. It was stored on the ground level and was hanged to the
required floor by tower crane. |
|
|
|
The
advantage is a fine quality finished facade achieved by such
pre-fabrication method. On the other hand the problem of water
leakage with this type of construction is primarily dealt with by
the overhanging toe of the whole prefabricated unit which stops
water penetration from the horizontal parts. |

|
Precast
Staircase |
|
The
precast staircase was constructed in 8 risers. The half landing was casted separately as
in-situ
part. Due to the smooth surface quality, no applied finishes would
be necessary. A metal nosing strip was the only thing that was
required to finish the stair. Naturally, construction waste was not
arised. |
|
|
|

|
Precast
Cooking Bench |
|
Cooking
benches were also pre-fabricated elements. Bench top was cladded with
1 piece 0.8mm satin finish stainless steel sheet. The bench itself
was of lightweight concrete and supported by 60mm concrete support,
smooth finish and epoxy painted. |
|
The
stainless steel sink was cast in lightweight concrete bed, 75mm
thick, to afford strength to stand chopping and cutting. Earthing
lugs were designed and built for both sink and bench. |
|

|
Prefabricated
Doorsets |
|
Prefabricated
door frames and doors were used in this project. These doorsets saved temporary timber support for door frame, thus reducing waste. |
|

|
Contact
of Contractor
|
|
Shui
On Building Contractors Ltd. |
12/F,
New Kowloon Plaza, 38 Tai Kok |
Tsui Road,
Tai Kok Tsui, Kowloon
|
Tel:
(852) 2398 4888
|
Fax:
(852) 2396 4113
|
|

|
|