Notable Features |
|
|
 |
Wastage level
and targets |
 |
Prefabricated
bathroom modules |
 |
Precast
cladding panels |
 |
Prefabricated
stair and lifts |
 |
Prefabricated
roof panels |
 |
Adaptability |
 |
Basic Information |
|
Location: |
Southern end of Greenwich peninsula
site, London, UK |
Building Type : |
Residential, and
mixed |
Contract
Period: |
Construction of phase 1 started in December 1999-Phases over a
five-year period |
Contract Sum : |
Approximately
£250 million |
Site Area : |
13
hectares (32.3 acres)? |
Gross Floor Area : |
|
Typical Floor Area
: |
|
Client : |
Greenwich Millennium Village Ltd, a joint venture development between
Countryside Properties Plc and Taylor Woodrow Plc. |
Housing associations
: |
Moat Housing Association, Ujima Housing Association |
Architect
: |
Ralph Erskine (master plan) with the support of EPR Architects (phase
1), Proctor Matthews Architects (phase 2). |
Landscape architects: |
Randle Siddley Associates, Robert Rummy Associates |
Planning consultant: |
Montagu Evans |
Innovation consultant: |
Richard Hodkinson |
Cost consultant
: |
WT
Partnership |
Environmental engineer: |
Taywood Engineering |
Structural engineer: |
Waterman Partnership, Thorburn Colquhoun |
Services engineers: |
WSP,
Thorburn Colquhoun |
Quantity surveyor: |
|
Main contractor: |
|
 |
. |
Overview |
|
The Greenwich
Millennium Village is part of the Greenwich Peninsula Development which includes
the Millennium Dome, 3,000 homes, 50 acres (20 hectares) of parkland, an
ecological park, a commercial area and transport links. |
|
This
residential development including 1377 homes (298 houses and 1079 apartments),
ranging from one-bedroom apartments to penthouses, is designed to set national
standards for future developments, minimizing environmental impacts and
maximizing sustainability. The development also includes a community center, a
primary school, a health center, shops, cafes, bars, and offices. |
|
The first phase
of the development comprises 100 apartments at the northernmost part of the site
beside the Thames and a new lake. The second phase comprises a mixture of
two-or-three storey houses with gardens, arranged in ribbon fashion, together
with 1,2, and 3 bedroom apartments arranged around the garden squares
Factory
produced modules: bathrooms, cladding panels, plant rooms, services risers,
stairs and lifts. |
 |
|
Prefabricated
Bathrooms
Units |
|
The units
were delivered as complete rooms fully fitted to include all services that are
pre-commissioned. The units were standardized in size and configuration although
some flexibility in final specification was available to meet consumer
selections. The units were made from structural steel framing to which were
fixed lightweight metal supports for plasterboard. |
|
 |
|
Precast
Staircases |
|
Precast
concrete stairs give early safe access to work areas. |
|
 |
|
|
![]() |
|
Wastage
Level
and
Targets |
Source:
http://greenwich-village.co.uk |
|
With 40% of
UK waste arising from construction an important concern is to reduce the amount
of waste arising from construction sites. Measurements of skip volumes removed
from sites showed typically 50m3 of construction waste per dwelling. There was a
continuous waste audit. One of the targets was to reduce construction waste
generation by 50%. |
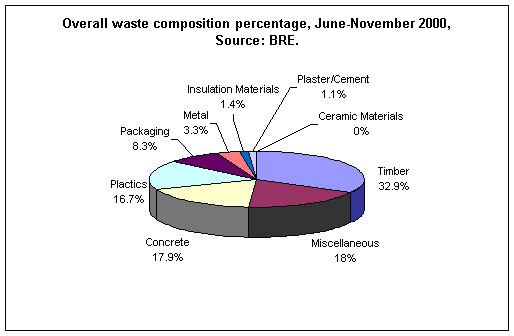 |
Improvement
benchmarks table
(source:
http://greenwich-village.co.uk) |
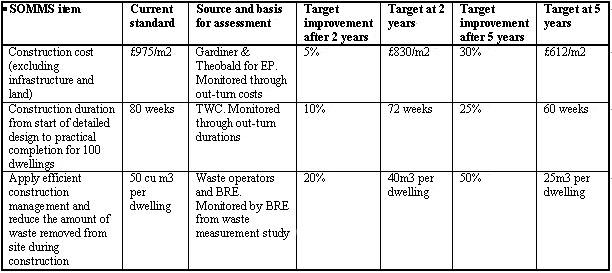 |
 |
|
Cladding
Panels |
Cladding panels were factory made to provide early
weather tightness to the building to allow early internal fit out. The panels
were 1-storey height and 6m long. The panels were made in two parts (source:
http://greenwich-village.co.uk): |
|
- The
first part comprises a backing panel to form the inner leaf of the elevation.
This panel forms the weather tight layer and has windows fitted within the
panel comprising a metal or timber frame, insulation and plywood to form the
internal and external surfaces. These panels are very simple and quick to
erect and form the vertical weather tight enclosure.
|
- The
second part comprises a rain screen made from a variety of materials including
timber cladding, terracotta tiling, and colored cement fibre panels. As rain
screen these materials are fixed later in the construction process to provide
the external appearance.
|
 |
|
Prefabricated
Roof
Panels |
|
Complete
factory made roof panels with roof drainage outlets built in. These provided
early weather tightness of the building together with the cladding panels. |
 |
|
Adaptability |
|
“Buildings need to change to meet the changing needs of their
occupiers”. The adaptability concepts provides long life span of the
building structure and therefore avoid demolition of the whole
building. Several design solutions were reviewed to give greater
levels of adaptability such as: |
|
-
Steel framed structures that are pre-engineered with standardized
connections, grid layouts and arrangements that allow for later
change. In standardizing the connections, a variety of different
structural members from a kit of parts can be assembled together and
modified over time in the same way.
|
-
The internal walls are dry wall systems comprising metal framing
with several layers of dense plasterboard. The dry wall system
avoids wet trades and therefore minimizes construction waste
generation.
|
-
Services are distributed throughout the buildings from a central
core that provides sufficient capacity for future needs. On a
floor-by-floor basis, the layout and capacity of services is
designed specially for later adaptation. E.g., structured cladding
for information systems is used throughout the apartments which
gives massive data capacity with large number of outlet positions.
|
-
Cladding systems that are factory made panels able to be quickly
interchanged to meet different requirements.
|
Web
site:
http://greenwich-village.co.uk |
|
 |
|